PCB Prototype: Choosing An Agile Services Provider
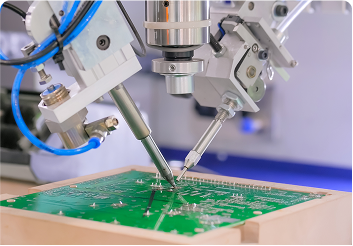
Introduction: PCB Prototype The demand for high-quality printed circuit board (PCB) prototypes is ever-increasing. Companies that specialize in PCB prototyping face the challenge of meeting rigorous quality standards while also delivering products swiftly. For businesses in sectors such as aerospace, defense, medical, and industrial automation, selecting the right PCB prototype provider can significantly impact their […]
PCB Assembly: Selecting the Right Supplier for Complex Needs
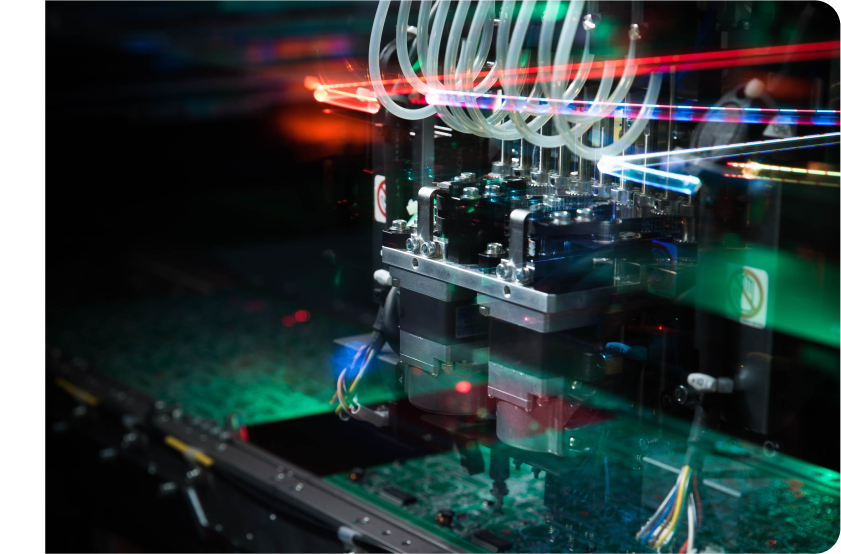
Introduction: PCB Assembly In the dynamic world of electronics manufacturing, the importance of high-quality printed circuit board (PCB) assembly cannot be overstated. Companies often find themselves in situations where they must meet tight deadlines, navigate complex technical requirements, and ensure superior product quality. This blog will explore the critical factors involved in choosing the right […]
Quick Turn PCB Assembly: Maximizing Efficiency and Quality
Introduction to Quick Turn PCB Assembly In today’s fast-paced electronics industry, quick turn PCB assembly has become a vital service, enabling companies to meet tight deadlines without sacrificing quality. Quick turn PCB assembly refers to the expedited process of producing printed circuit boards (PCBs) from design to final product. This service is essential for various […]
PWB Board: Crucial Guide to Further Learnings
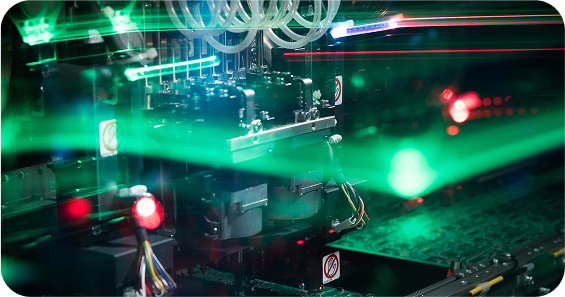
PWB Board: Introduction Printed Wiring Boards (PWBs) are crucial components in the electronics manufacturing industry. Their functionality and reliability are paramount, as they form the backbone of various electronic devices across industries like aerospace, defense, medical, and automotive. To ensure high performance and durability, several assembly support activities are necessary. These activities include component sourcing, […]
PCB Board Manufacturer USA: Essentials For Industry
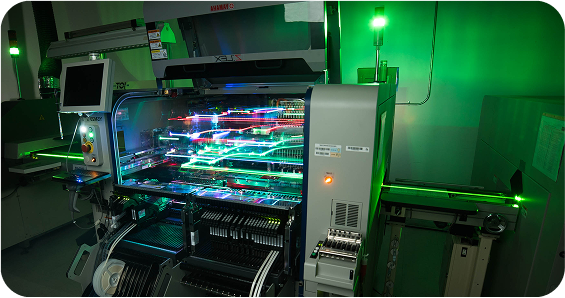
PCB Board Manufacturer USA: Introduction PCBs, or printed circuit boards, are the backbone of modern electronic devices, playing a pivotal role in industries ranging from aerospace to medical devices. As demand for precision electronics continues to rise, the importance of partnering with a reliable PCB board manufacturer USA becomes increasingly evident. These manufacturers provide essential […]
Printed Circuit Board Prototype: Quick Turn Quote Guide
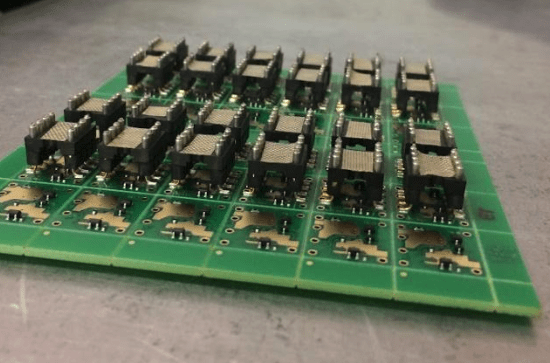
In manufacturing, the process of developing a PCB printed circuit board prototype demands precision, speed, and seamless integration across multiple stages. The process from the initial RFP request for a proposal to receiving a quote involves important steps to ensure a quick and accurate response. This guide explores the essential steps to generate a quick […]
Prototype Circuit Board: Quick Turn Fundamentals
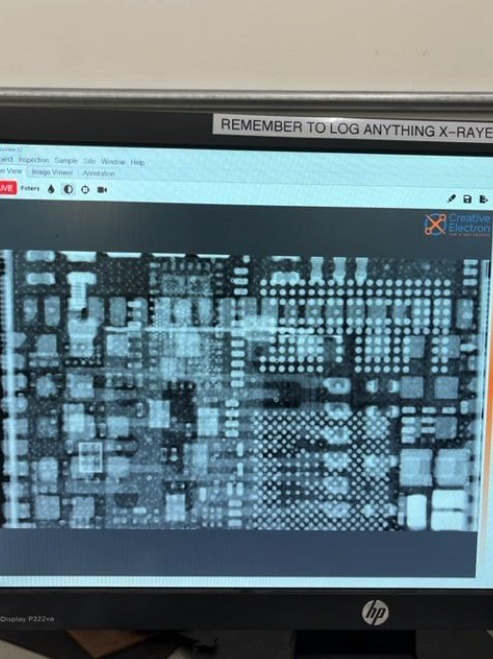
Introduction: Prototype Circuit Board Developing a prototype circuit board (PCB) is a critical step in the product development cycle, especially for high-stakes industries like energy and aerospace. Ensuring a defect-free, on-time delivery is imperative. Effective planning and the right methodologies can result in significant cost and time savings, making the quick-turn process indispensable for businesses […]
Printed Circuit Board Assembly: What to Look For?
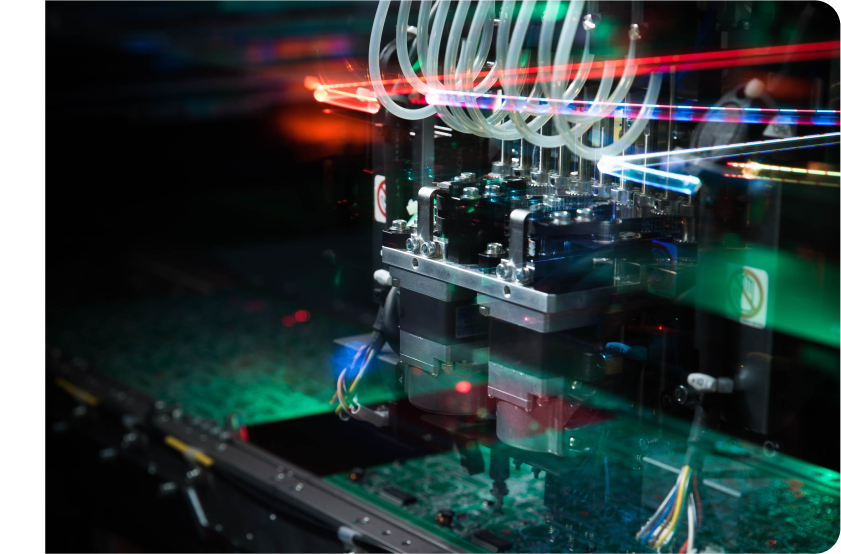
Introduction In today’s highly competitive manufacturing landscape, the demand for reliable printed circuit board assembly (PCBA) services has surged. Companies across various industries, including aerospace, defense, medical, and automotive, are increasingly outsourcing their PCB assembly needs to specialized providers. This blog will explore five key reasons why companies seek out PCBA services, providing example illustrations […]
PCBA: Speed, Technology, and Continuous Improvement
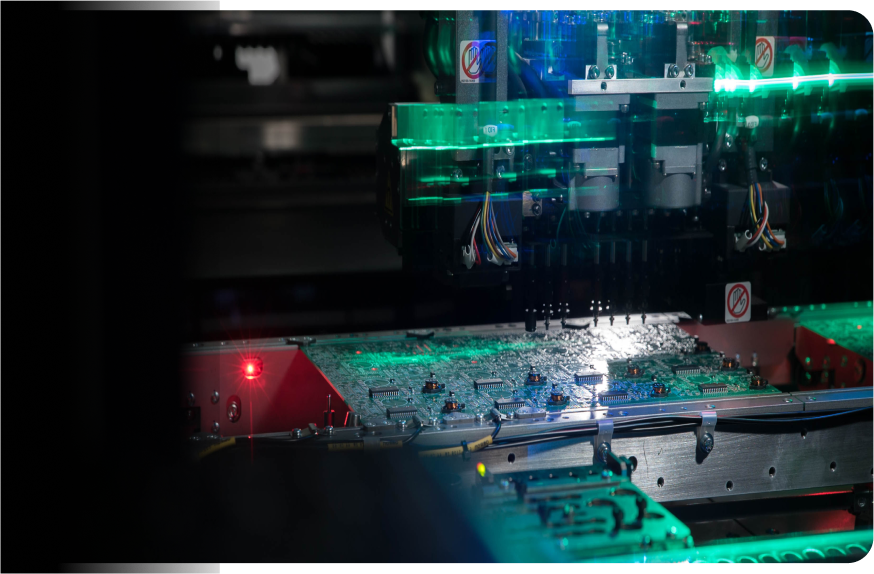
Introduction Printed Circuit Board Assembly (PCBA) is a critical process in the manufacturing of electronic devices, requiring precision, reliability, and innovation. Leaders in this field stand out by focusing on several key aspects that ensure their services meet the highest standards. These include a quick turnaround on assembly, state-of-the-art machinery, equipment well-suited for cutting-edge and […]
Electronics Manufacturing: PCA Advanced Capabilities Uncovered
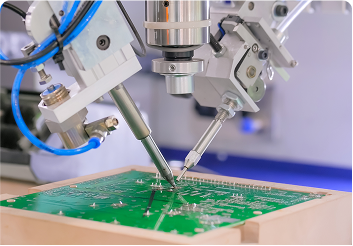
Introduction In the fast-paced world of electronics manufacturing, having a reliable partner with a broad range of manufacturing capabilities is crucial. From the initial design stages to the final assembly, each step requires precision, expertise, and advanced technology. This blog explores the various capabilities that are essential in electronics manufacturing, emphasizing the importance of each […]