Circuit Card Assembly: The Key to Advanced Manufacturing
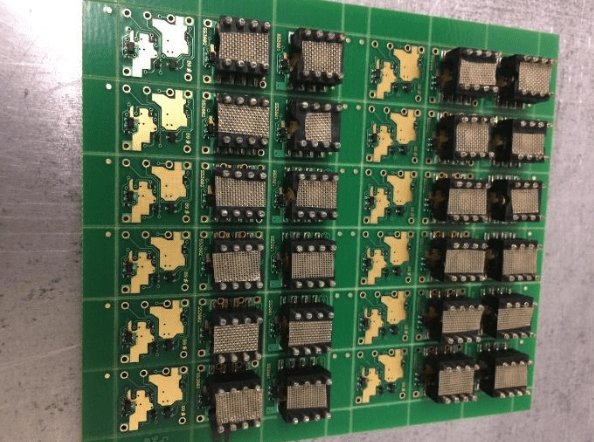
Introduction Circuit card assembly (CCA) is a crucial component in the manufacturing process for numerous industries, including aerospace, energy, and startup technology companies. As these sectors strive to develop new products, the demand for quick-turnaround, high-quality printed circuit board (PCB) assembly services has never been higher. The New Product Introduction (NPI) processes, prototyping, testing, and […]
High Speed PCB: The Value of Assembly Support Activities
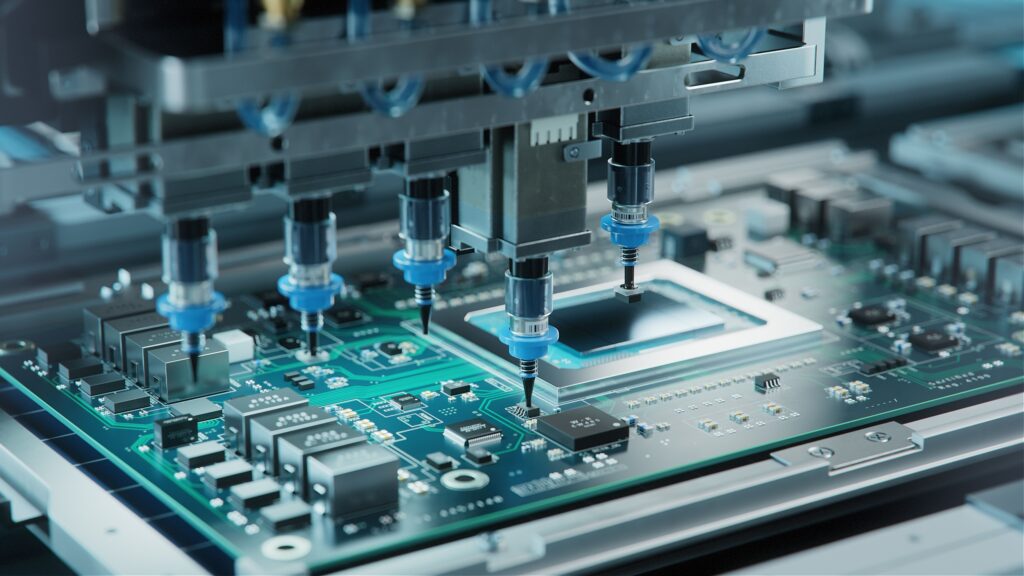
Introduction to High Speed PCB The rapid evolution of technology and the increasing demand for sophisticated electronic devices have significantly impacted the manufacturing processes of high-speed printed circuit boards (PCBs). High speed PCBs are critical components in a wide range of applications, including telecommunications, aerospace, automotive, and industrial automation. These PCBs must meet stringent performance […]
PCA Supply Services: Enhancing Manufacturing Efficiency
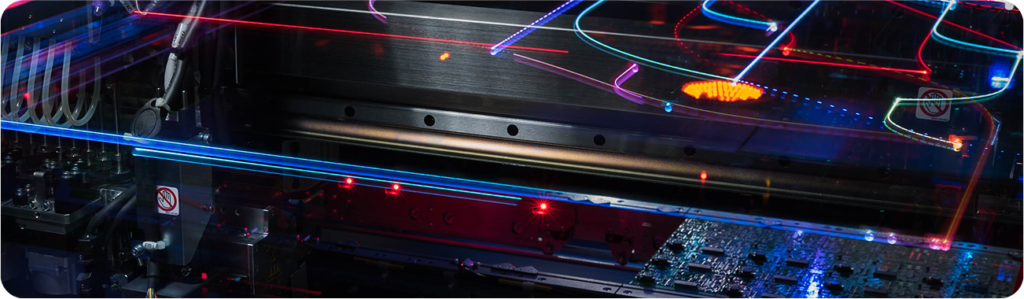
PCA Supply Services Introduction Precision electronics assembly services (PCA supply services) are critical for industries like aerospace, defense, medical, automotive, and industrial automation. These sectors demand high-quality components, often customized to stringent specifications, to ensure reliability and performance. This blog explores the benefits and offerings of PCA supply services, emphasizing quick-turn prototyping, mid-volume production, and […]
Printed Wiring Assembly: Unearth the Power of Specialization
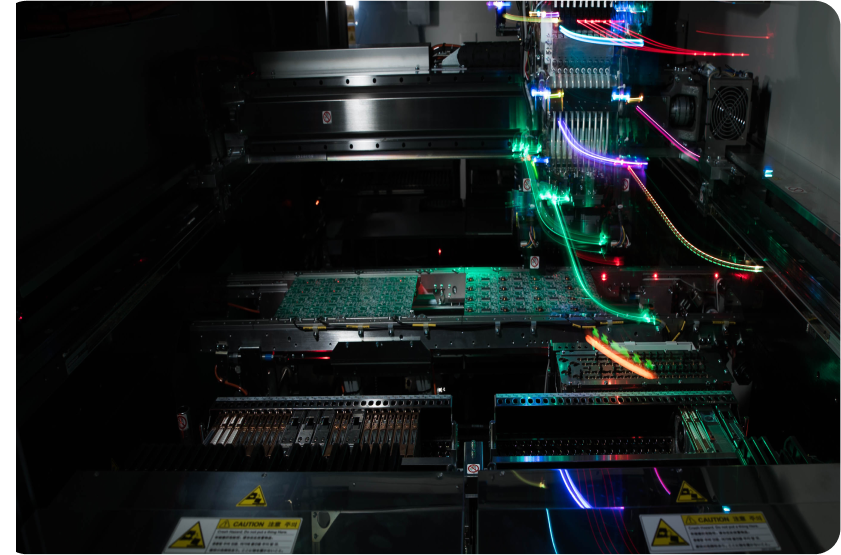
Printed Wiring Assembly Introduction Printed wire assembly (PWA) is a crucial component in various industries, including aerospace, defense, medical, and automotive sectors. As technology continues to advance, the demand for specialized and reliable printed wiring assemblies has never been greater. Companies in these industries are increasingly seeking partners rather than mere suppliers for their printed […]
PCB Prototype Board: Insights in Aerospace and Energy
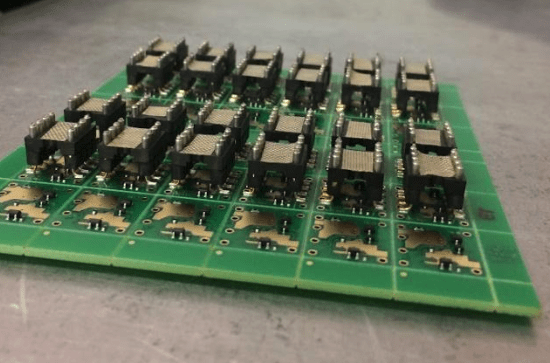
Introduction to the PCB Prototype Board In the realms of aerospace and energy, precision and reliability are paramount. The industries rely heavily on advanced electronics, where PCB (Printed Circuit Board) prototype boards play a crucial role. From initial design to final product, these prototype boards are integral to ensuring functionality and performance. This blog delves […]
Flex PCB Manufacturer: New Solutions for Industry Needs
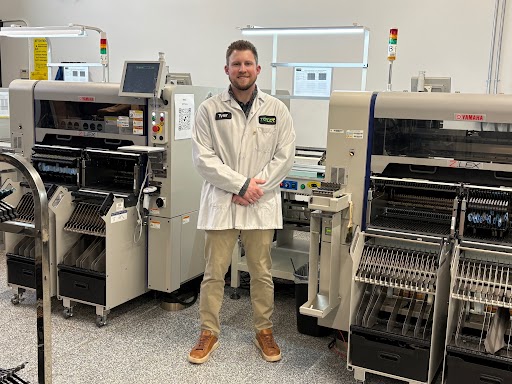
In today’s highly competitive and technologically advanced industries, flexibility and innovation in design and manufacturing are critical to staying ahead. A flex PCB manufacturer plays a pivotal role in providing solutions that cater to the demands of cutting-edge and high-complexity applications across various sectors. This blog explores the significance of flex PCBs, the benefits they […]
BGA Soldering: Your Ultimate Guide for Essentials
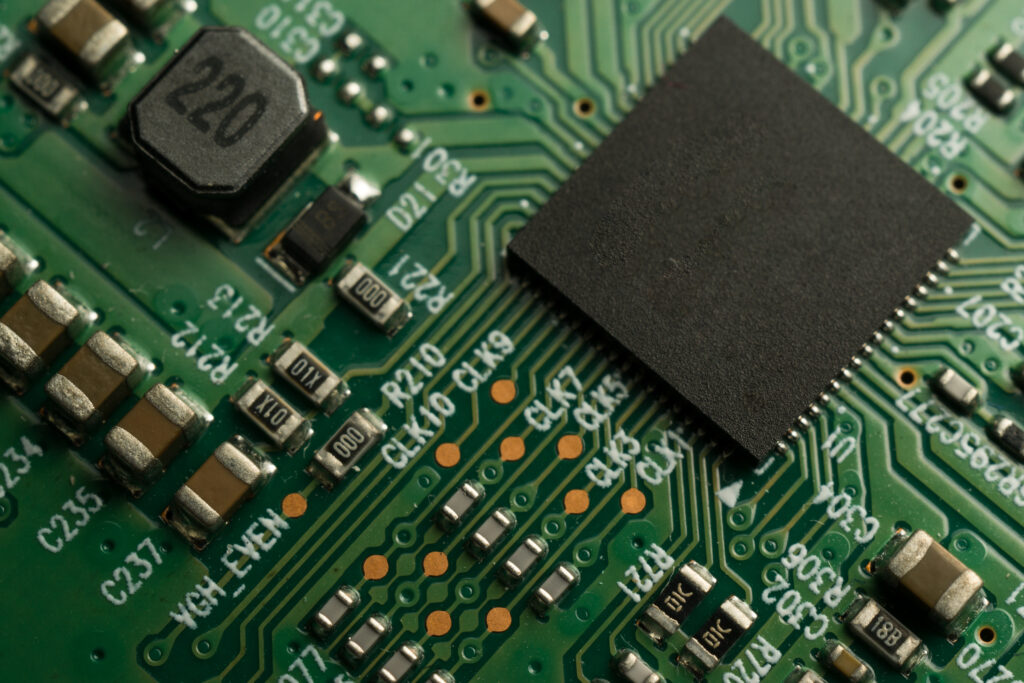
Introduction Ball Grid Array (BGA) soldering is a critical technology in the assembly of printed circuit boards (PCBs), particularly for applications in aerospace and energy sectors. The high-density, reliable connections provided by BGA soldering make it indispensable in these fields where performance and durability are paramount. This guide aims to provide a thorough understanding of […]
PCB Manufacturers Near Me: What Differentiates Them?
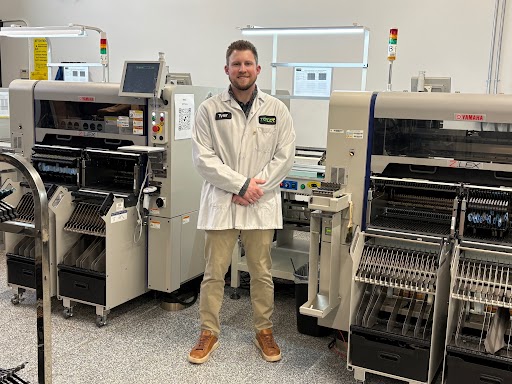
When searching for “PCB manufacturers near me,” you may initially think proximity is the most important factor. However, there are several other critical aspects that set top-tier PCB manufacturers apart from their counterparts. Whether you are a program manager, electrical engineer, supply chain manager, PCB designer, hardware engineer, manufacturing engineer, or NPI director, selecting the […]
Electromechanical Assembly: Learn From a PCB Assembler’s POV
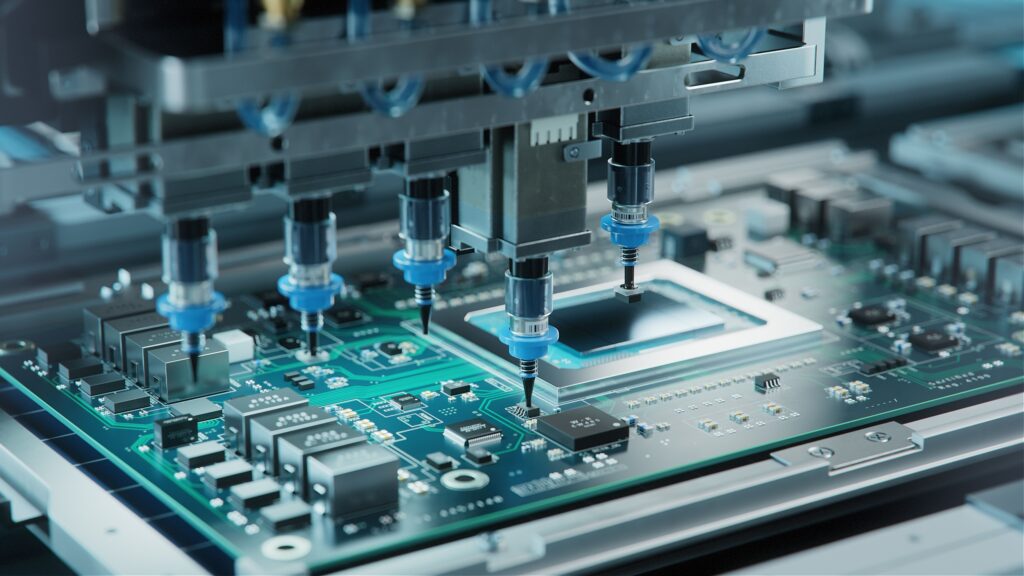
Introduction Electromechanical assembly stands out as a critical process that combines electronic and mechanical components to produce highly functional devices. As demand for sophisticated and reliable products surges across industries such as aerospace, defense, medical, and automotive, the importance of ensuring top-notch quality in electromechanical assembly becomes paramount. From a printed circuit board assembler’s perspective, […]
Flying Probe Test: Understanding PCB Quality
Particularly in the assembly of printed circuit boards (PCBs), ensuring the quality and functionality of the final product is paramount. Among the various testing methodologies employed, the “flying probe test” stands out due to its efficiency and effectiveness. This comprehensive guide delves into the details of the flying probe test, explores the concept of impedance […]